コラム
導入時の検討ポイントや、活用方法な選び方など防犯カメラなどのお役立ち情報をご案内いたします。
Column
コラム
構内物流とは?役割やあるべき姿を実現するための改善策を解説
2025年7月4日(金)
構内物流の概要や役割、業務内容など網羅的に解説しています。構内物流は、工場や倉庫の業務の効率に関わるため、工場業務の改善や効率アップに興味のある方は参考にしてください。
構内物流とは、工場や倉庫内で行われる物品の受け入れ・保管・搬送・出荷といった一連の物流作業のことです。現場の作業効率や生産性に大きな影響を与える重要な業務です。
工場や倉庫現場では、人員不足・物流量増加による業務効率化が急務となっています。構内物流の改善に取り組まないと、今後業務遂行に悪影響を及ぼすかもしれません。
この記事では、構内物流の概要や役割、業務内容、改善策など網羅的に解説しています。記事を最後まで読めば、構内物流の重要性や改善するために何をすれば良いのかがわかります。
構内物流について知りたい、工場・倉庫内の労働環境改善に取り組みたいと考えている方は参考にしてください。
構内物流とは
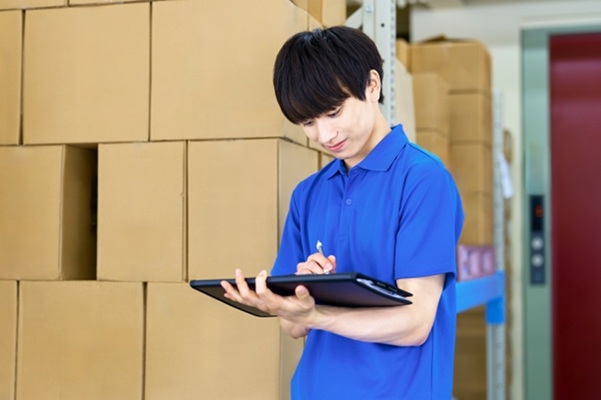
一般に、物流は「調達物流(工場への搬入)」「販売物流(出荷・配送)」「回収物流(リターン・リサイクル)」の3種類に分類されます。構内物流とは、調達物流と販売物流の中間に位置し、工場内の物流全般をになっている業務です。
具体的には、資材や部品の受け入れから始まり、製造ラインへの供給、完成品の保管や出荷準備に至るまでの流れを指します。
従来は物流業務を手動で行うのが一般的でしたが、近年自動化・機械化が進み、ほとんど人の手を借りずに搬入から出荷まで行う工場や倉庫も存在します。構内物流は、製造現場の効率化や生産性の向上に密接に関わる業務です。その最適化は企業の競争力強化にも欠かせない要素といえるでしょう。
構内物流の役割
構内物流の役割は以下の3つです。
- 業務全体を効率化する役割
- 作業者を支援することで生産ラインに集中させる役割
- 生産全体の流れを支える中枢としての役割
順番に解説していきます。
業務全体を効率化する役割
構内物流は、工場内の動線を整え、資材や製品の移動を無駄なく行うことで、全体の業務効率を高める役割を担います。例えば、必要な資材が必要なタイミングで現場に届けば、作業が止まることなくスムーズに進行します。
そのためには、在庫の場所や数量、使用タイミングを正確に把握し、過不足なく動かすための仕組みづくりが不可欠です。
近年では、在庫管理の自動化やフローの可視化といった取り組みも進んでいます。自社の工場・倉庫内のスペースに適した方法で、効率を最大限まで上げられる方法を見つけましょう。
作業者を支援することで生産ラインに集中させる役割
構内物流は、現場の作業者が本来の業務に集中できるようにサポートする役割もあります。資材を必要なタイミングでピンポイントに届けたり、完成品を即時に回収したりすることで、作業者は移動や確認といった間接作業に時間を取られなくなります。
また、従業員が資材の取り違いや混在を防ぐことで、作業ミスの削減や品質の安定にもつながります。ミスによるやり直しが減れば、全体の作業時間も短縮されるでしょう。構内物流の精度が高まれば、作業者が安心して集中できる現場環境づくりにもつながります。
生産全体の流れを支える中枢としての役割
構内物流は、工場全体の生産リズムを支える中枢的な存在でもあります。
構内物流の完成形の具体例として「ジャストインタイム方式」が挙げられます。ジャストインタイム方式とは、必要なものを必要なタイミングで、過不足なく供給する体制です。生産ラインの停滞や在庫の偏りを防ぎ、効率的で安定した生産を実現できます。
ジャストインタイム方式を実現するには、各工程との連携を密にしながら、搬送や供給の精度を高めることが不可欠です。そのためには、工場や倉庫の物の流れをリアルタイムに把握しておかなければいけません。
そこで、体制を整えるには一定のシステム投資が必要になります。
構内物流の業務内容
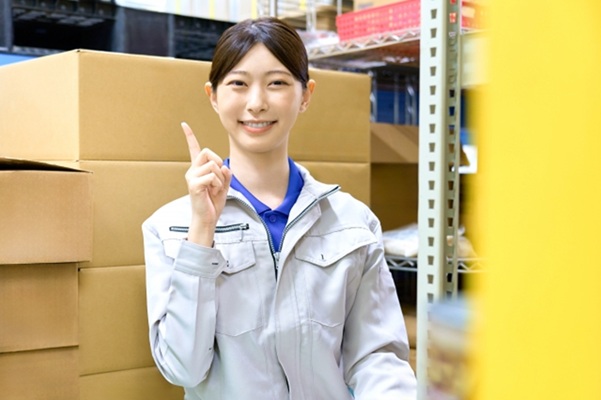
構内物流の業務内容は以下の5つに分けられます。
- 入庫・受け入れ
- 保管
- 出庫(ピッキング)
- 搬送
- 出荷
順番に解説していきます。
入庫・受け入れ
仕入れた資材や部品などが物流拠点に到着した後、まず行われるのが受け入れ作業です。受け入れは、届いた物品の種類や数量が正しいかを確認する工程で、その後、物品を決められた保管場所へ移す入庫作業に移ります。 入庫・受け入れの工程では、積み下ろしなどの重労働が発生しやすいため、デパレタイザーやフォークリフトなどの搬送機器を活用することで、作業の効率化と負担軽減が可能です
保管
保管業務では、入庫した物品の品質が落ちないよう適切に管理することが求められます。種類、ロケーションや数量を正しく管理し、欠品を防ぎ、すぐに取り出せるようにします。
例えば、出荷頻度の高い商品を奥に保管してしまうと、作業効率が低下してしまうでしょう。逆に、似た商品を近くに置くとピッキング時のミスが起こりやすくなるため、保管場所の選定は重要です。
近年では人の手による正確な管理が難しいことから、在庫管理システムなどを用いた管理や、AIカメラによるパレットラックの空き状況検知などにより効率化を図る例もあります。
出庫(ピッキング)
ピッキングは、指示書をもとに製造現場に必要な物品を取り出す作業のことを指します。タイミングよく、正しい品を正確な数量で取り出すことが求められるため、正確性や素早さが重視されます。
保管場所が広ければ広いほどピッキングを行う従業員の負担は大きくなり、経験の少ない従業員は商品の保管場所がわからず時間がかかりやすいです。保管作業と同様、効率化のために在庫管理システムを活用して行われる場合があります。
搬送
搬送とは、工場内で資材や製品を工程ごとに移動させる作業です。生産フローのさまざまな場面で発生する重要な工程のひとつです。
搬送を人の手で行うと、広い工場や倉庫内を重量物を持ったまま移動しなければいけません。そのため、周囲の確認がしにくく、棚に商品をぶつけたり、腰を痛めたりするリスクがあります。
工場内を動き回る負担を減らすことや搬送中の物品の損傷を防ぐ目的で、フォークリフトやコンベアなどの機器を活用すると効率化が図れます。
出荷
出荷は、工場で作られ保管されている製品を引き渡す作業です。出荷にともない、製品の仕分けや梱包をして荷姿を整える準備も必要です。
入荷時同様、フォークリフトやパレタイザーを使うことで負担軽減につながりますが、ロボットや自動倉庫システムでも負担を減らし、効率アップを図れます。
構内物流の課題
構内物流が抱える代表的な課題として、「人手不足」や「荷積み・荷下ろしの負担」が挙げられます。なかには、2030年の日本の社会や経済に大きく影響されると言われている2030問題(生産年齢人口の大幅減少など)に直結した課題もあるため、早急な改善が求められています。
構内物流に関する課題について詳しく解説していきます。
情報管理に関する課題
構内物流では、物品の種類や在庫数、保管場所などの情報を常に正確に管理する必要があります。しかし、品目が多様化する工場では、在庫に関する情報が属人的に扱われていたり、システムが導入されていなかったりするケースも少なくありません。
結果として、誤出荷や在庫の過不足、ピッキングミスといったエラーが発生しやすくなります。エラーが発生するたびに出庫・搬送作業の停滞や生産ラインの遅延を招く恐れがあるため、作業効率は悪化していきます。
また、作業指示や業務フローが曖昧なまま進むと、ヒューマンエラーを助長し、業務品質面でもリスクが生じかねません。ベテラン従業員頼みの現場体制を見直し、情報管理のデジタル化や業務の標準化が必要です。
人材・労働力に関する課題
少子高齢化の進行にともない、物流業界全体は慢性的な人手不足に直面しています。構内物流においても、体力的な負荷の高さや拘束時間の長さといった要因により、若年層の定着が難しく、高齢化が進んでいる現場も見られます。
新人の定着が進まない結果、業務の属人化が進み新人教育や引継ぎが難しくなり、現場の持続性にも影響を及ぼしかねません。人材が不足すると、一人あたりの業務負荷が増し、作業スピードや正確性の低下、さらには離職率の上昇といった悪循環に陥る恐れがあります。
人手不足を抜本的に改善するには、自動化や機械化によって重労働を減らし、若手が定着しやすい職場づくりを進める必要があります。
作業環境・安全性に関する課題
構内物流の現場では、荷積み・荷下ろしといった肉体労働や重機の操作をともなう作業が多く、作業者にとって大きな負担です。フォークリフトやパレット搬送などに高度な技術を要する場合は、作業品質や所要時間に個人差が出やすく、工程全体の作業量の安定化が難しいです。
さらに、安全対策が不十分な現場では、労働災害のリスクが高まり、重大事故につながる恐れも否定できません。
拘束時間の長さや作業場の整理不足といった環境面の課題も含めて、作業者の安全と健康を守る仕組みづくりが強く求められています。労働環境が改善されれば、従業員の不満やストレスが軽減でき、定着率の向上ややる気アップにつながるでしょう。
構内物流を改善する流れ
構内物流を改善する流れは以下のとおりです。
①現状の分析・課題の洗い出しを行う
②製造現場の効率化を図る
③構内物流全体の改善に取り組む
効率化を図る方法や改善に取り組むべき内容は多岐にわたるため、内容により小分けにして解説していきます。
倉庫作業を効率化する方法は以下の記事でも詳しく解説しています。
倉庫作業を効率化する11の方法を解説!必要な理由やポイントを紹介
①現状の分析・課題の洗い出しを行う
構内物流の改善を行う最初のステップとして、現状の作業フローや作業内容を分析し、課題を正確に把握することが重要です。分析を行う際は、工場内で使われている作業マニュアルや配属に関する資料を確認するだけでなく、現場を回ることで構内物流全体の状態を細かく把握できます。
さらに、防犯カメラを工場内に設置し、分析に活用することで作業動線や人の動きも客観的に可視化できるようになります。効率的な課題分析が可能になるため、おすすめです。
工場や倉庫での防犯カメラの活用法については以下の記事で詳しく解説しています。
工場・物流倉庫向け防犯、監視カメラソリューション|株式会社稲沢商会
②製造現場の効率化を図る
課題の発見ができたら、製造現場の効率化を図ります。具体的な効率化方法として以下の4パターンを紹介します。
- 作業フローや配属を見直す
- スペースを整理する
- 業務用の備品の支給・見直しを行う
- マニュアルを作成・修正する
順番に解説していきます。
作業フローや配属を見直す
現状の作業フローや配属人数を見直し再設定することで、人的ミスや業務負担を減らせます。例えば、梱包方法の変更で所要時間を短縮したり、時期や繁忙度に応じて人員を柔軟にローテーションさせたりする工夫が有効です。
また、人の入れ替えによって負担が一部の作業者に偏るのを防ぎ、やる気の低下や人的ミスの頻発の解消にもつながります。
人員配置の調整には、防犯カメラの記録を参考にすると、従業員の動きから動線や作業状況を客観的に把握しやすくなります。
スペースを整理する
資材や製品を仮で保管しているスペースや、使われていないスペースを整理することで業務の効率化や業務負担の軽減が可能です。未使用の場所を、業務用スペースとして活用する、正式な保管スペースとして拡張するなどして、より働きやすい環境に整えましょう。
加えて、スペースが整理できなかった原因や今後のルールを明確にすると同じミスの発生を防止できます。
また、物品が定位置に戻されておらず通路に放置されていると、ピッキングや搬送の邪魔になるため、通路スペースを常に確保しておくことも作業効率の向上につながります。
業務用の備品の支給・見直しを行う
ハンディターミナルの導入により、ピッキングや搬送業務の効率化や人的ミスの削減が期待できます。必要以上に設置された台車や使いにくい形状の備品はスペースを圧迫するため、数や形状の見直しも重要です。
備品の支給には一定のコストがかかるため、費用対効果を考慮し、購入する物品を選定しましょう。
AIカメラを活用すれば、従業員による備品置き場からの備品の持ち出しの検知、および製造ラインへの備品の置き忘れの検知が可能です。手間になりがちな備品の管理を効率化できるとともに、見直しにも活用できます。
マニュアルを作成・修正する
手順が明確でない業務があると、手順の確認に時間がかかります。誰でも理解できる形でマニュアルを整備し、視覚的にわかりやすく提示することで、人的ミスや業務の遅延削減につながります。
また、すでにマニュアルが作成されている場合も、現状の業務内容と異なる点がないか確認し、最新の情報に変更することが重要です。
新たに備品や機器などを導入した場合は、マニュアルも作成し、誰でも扱える状態にする必要があります。正しい扱い方を知らないまま、マテハン機器やロボットを扱うと事故や故障につながる可能性があります。
口頭説明だけでなく、マニュアルにより正しい手順と取扱いをいつでも確認できる環境を作りましょう。
③構内物流全体の改善に取り組む
作業環境や作業フローの見直しによって現場の効率化が進んだあとは、構内物流全体の最適化にも取り組む必要があります。例えば、在庫や搬送の管理にITシステムを取り入れることで情報の精度が高まり、ロボットを活用すれば人手不足や作業負担の解消が可能です。 さらに、物流の出入り口を管理する仕組みを整えることで、場内と場外の連携精度を高めることも構内物流改善の一環として有効です。工場や倉庫におすすめのITシステムやロボットについて詳しく解説していきます。
在庫管理システムを導入する
資材や物品の保管に管理システムを導入することで、構内物流の効率が大きく向上します。ピッキング時に物品を探す手間を減らし、欠品・過剰在庫などのミスを防ぐことも可能です。
また、各物品や製品の情報をわかりやすく整理できるため、業務が属人化しにくく、分担しやすくなります。これまで3時間かかっていた作業が2時間で終わるといった改善も期待でき、残業時間の削減や人件費の抑制にもつながるでしょう。
注意点として、在庫管理システムを導入する際は、工場の状況にあったシステムを選ぶ必要があります。在庫管理に防犯カメラを活用する方法については以下の記事で詳しく解説しています。
ロボットを導入する
業務補助を行うロボットを導入することで業務負担を大幅に減らせます。荷積みや荷下ろしといった重労働には、パレタイザーやデパレタイザーを活用することで労災の発生率の低下が望めます。
物品や製品の移動には搬送支援を行うロボットがおすすめです。地面の磁気テープやバーコードを識別しながら自走するタイプや、センサーにより周囲を認識し、目的地まで自走するロボットがあります。
導入にあたり、従来の作業フローの変更や導入コストの確認を行う必要があるため、現状の課題と照らし合わせて導入を検討しましょう。
配送を効率化する
構内物流の起点・終点となる出入り口の管理を最適化することで、誤配送や積み残しといったミスの防止や、待機車両の混雑回避といった効果が期待できます。
例えば、防犯カメラとナンバープレート認識システムを連携させれば、構内に出入りする車両の確認作業が自動化され、受け入れ体制の精度が向上します。
さらに、出庫準備の進行状況やスペースの空き具合などをリアルタイム映像で把握できれば、構内と構外の連携もスムーズになります。ネットワークカメラを複数拠点に設置すれば、電話連絡なしでも離れた現場の状況を目視で確認可能です。
出入り口管理の高度化は、業務の流れ全体を支える基盤として、導入価値の高い取り組みといえるでしょう。
まとめ
構内物流を改善するためには、現場の課題を確認し、効果的な施策を実施することが重要です。
改善施策としては、マニュアルの整備や人員配置の見直し、スペースの再活用など、比較的低コストで取り組めるものから、倉庫管理システムやロボットの導入といった高度な取り組みまでさまざまです。
中でも、コストを抑えつつ効率化を図る方法として注目されているのが防犯カメラの活用です。現場の動線や作業状況を「見える化」することで、作業効率の改善やヒューマンエラーの抑制、安全管理の強化に効果を発揮します。
さらに、AIカメラを導入すれば、従業員による備品の持ち出しや製造ラインへの備品の置き忘れを自動で検知でき、備品管理の効率化と見直しに役立ちます。また、パレットラックの空き状況を把握して保管効率を高めるなど、在庫管理の省力化にも効果を発揮します。
株式会社稲沢商会では、車両の入退場管理や在庫管理支援、巡回点検の効率化など、構内物流における幅広い課題に対応した防犯カメラ・AIカメラの導入提案を行っています。コストを抑えつつ構内物流全体の質を高めたいとお考えの方は、ぜひ一度ご相談ください。
アイデアを形にし、あらゆるニーズにお応えします
数多くの導入により積み重ねてきた実力。
そして、防犯に関する豊富な知識と経験のある防犯設備士の有資格者を揃えており、
お客様のニーズにあった安心空間のご提供をお約束いたします。
セキュリティ強化にお悩みの方、業務の効率化などお困りの方は、是非稲沢商会をご検討ください。
ネットワークカメラご検討の方 はこちら
お問い合わせ
販売パートナー募集
このページの上部へ